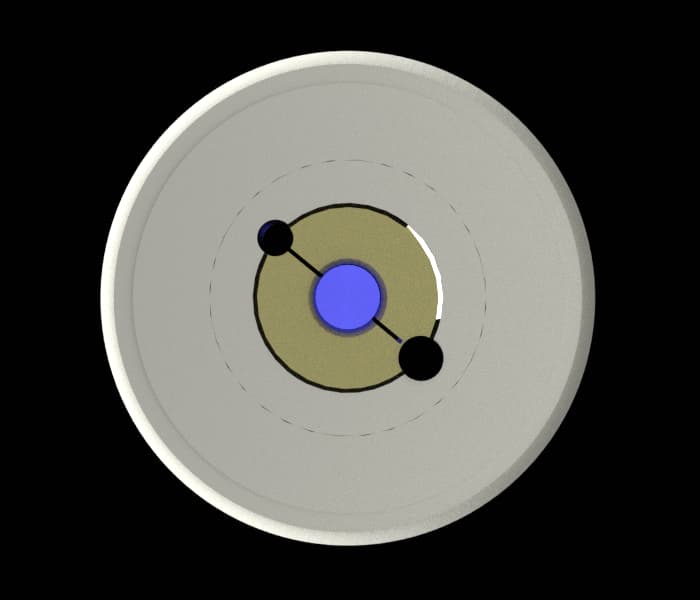
1. Improved hub-to-shaft concentricity.
Radial run out less than .001/.026 mm as assembled enables customers to attain higher drive speeds, reduce unwanted vibration, and maintain concentricity. The patented Concentric Maxi Torque connection system offers tight run out control, precise component positioning and eliminates the need for secondary machining; benefits not able in other connection devices such as keyways, set screws, pins and clamp collars.
See how the Concentric Maxi Torque improves hub-to-shaft concentricity.
2. Speed and ease of assembly.
Pulley and bushing are sold together as an assembly. There is a mechanical shrink fit affected by using a screw axial to the shaft, as a lever to force the tapered bushing into the matching taper in the hub. As the lever forces the two tapers together, the slot in the bushing is compressed, thus clamping the pulley to the shaft with a mechanical shrink fit. That same screw is removed and used on the opposite hole, which acts as a jack, releasing the shrink fit and allowing for removal or repositioning. Flexible positioning enables customers to easily phase, install, adjust and remove drive components, all while offering precise component positioning.
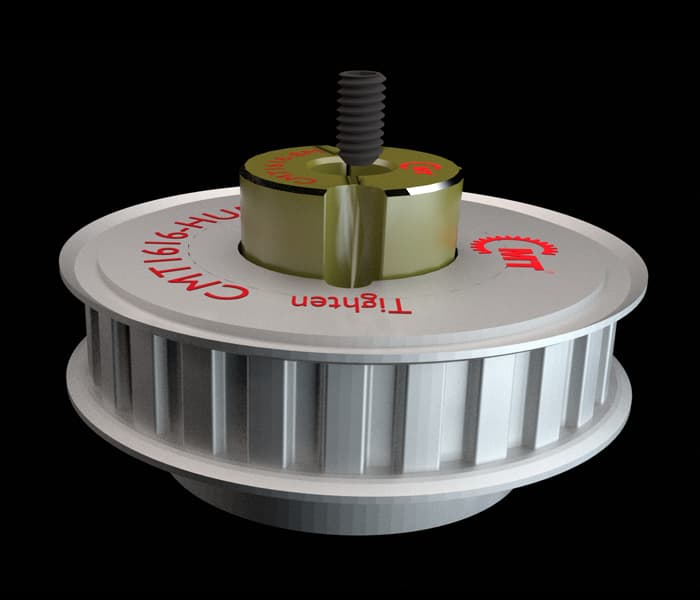
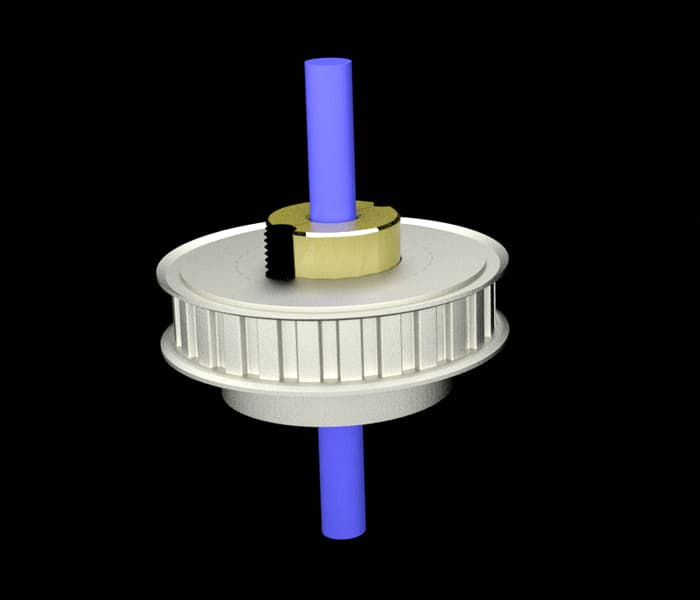
3. Provides uniform surface contact.
Ideal for applications requiring high-speed indexing and reversing, rotational
positioning accuracy, multiple assembly disassembly high reliability with minimal
maintenance. Flexible positioning enables customers to easily phase, install, adjust
and remove drive components, all while offering precise component positioning.
4. Reduced inertia.
As the machine speeds and indexing requirements continue to increase, reduction in inertia and vibration becomes important. Using the Concentric Maxi Torque system, components maintain their axial and radial position, reduce run out and increase machine efficiency. Reduced inertia results in increased power savings.
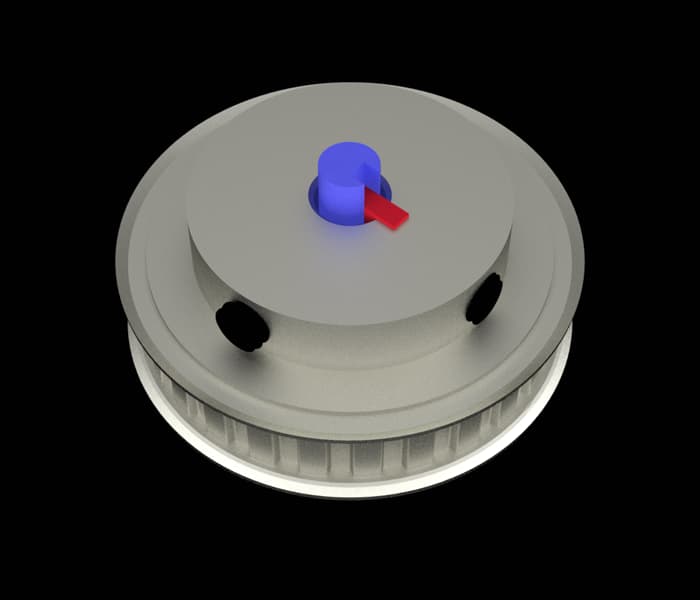
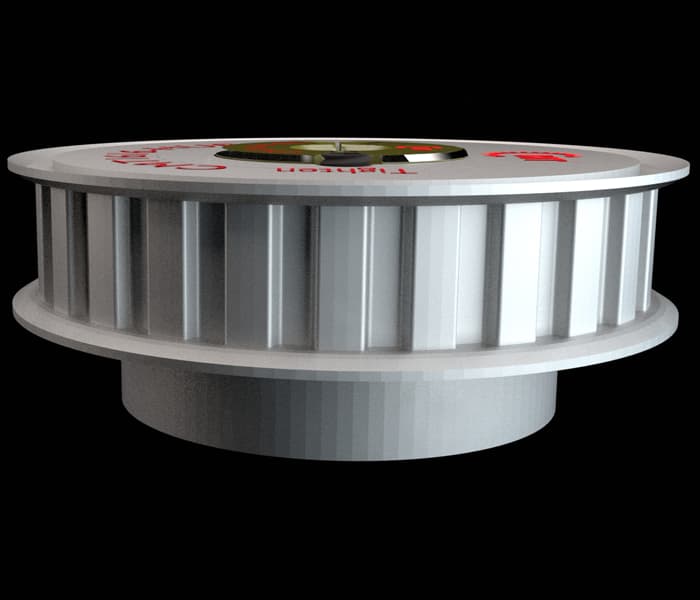
5. Compact design.
Keyways require additional machining of the shaft, adding cost and time. The Concentric Maxi Torque offers a compact design and a single screw eliminates the added cost of shaft modification and extended hubs often associated with the use of set screws or pins.
6. Lower maintenance costs.
Some machine builders rely on set screws to connect their components to the shaft. However, set screws can damage shafts and tend to loosen and slip during clutching and braking. Mechanical shrink fit providing uniform surface contact ensures no relative movement or loss of torque capacity over extended periods, reducing machine down time and maintenance costs.

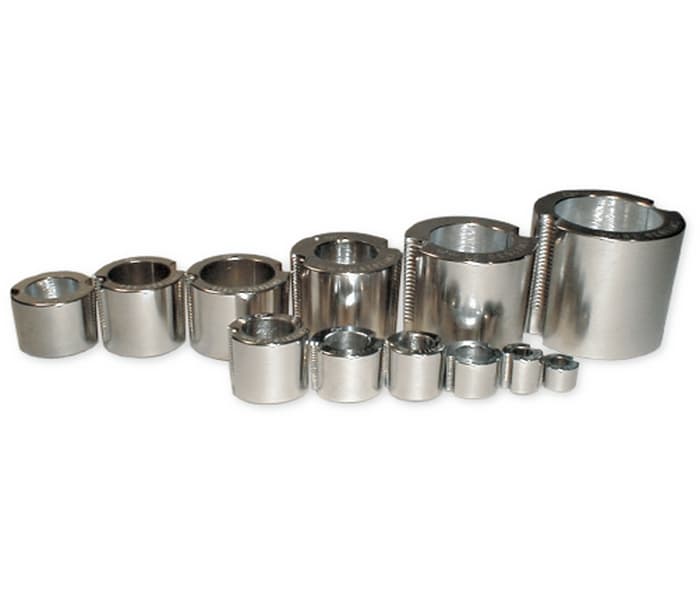
7. Various bore sizes.
Twelve sizes cover bores from inches 0.1250 (3mm) to 1.1875 inches (30mm) and torque capacities from 14 in-lbs (4Nm) to 2795 in-lbs (375Nm). Up to 15 English and Metric bore sizes per bushing size help lower inventory costs by enabling the same component to be used on multiple shaft diameter applications.