Early generation electric skateboards were plagued with so many inefficiencies that they threatened to relegate the whole industry to that of just another novelty. Grip, control and noise inconsistencies, cheap material construction, wheel durability issues, cumbersome designs, and poorly designed batteries were just a few of the problems.
Customer's Challenge
One Floridian innovator has made it his life's work to design and build the ultimate in custom, competition class electric skateboards and bring them to market.
Long Haired Boy Fine Electric Skateboards, LLC (LHB) is located in sunny central Florida, USA, with all products hand-assembled by owner/operator Damon Wood. “The truth is I just like to make things and get my hands dirty. That's why I've started down this long and fascinating road of bringing electric skateboard joy to central Florida and beyond.” – Damon Wood.
It's the marriage of art, advanced technology and an almost fanatical dedication to superior performance that has set this Long Haired Boy apart from today's mass production facilities.
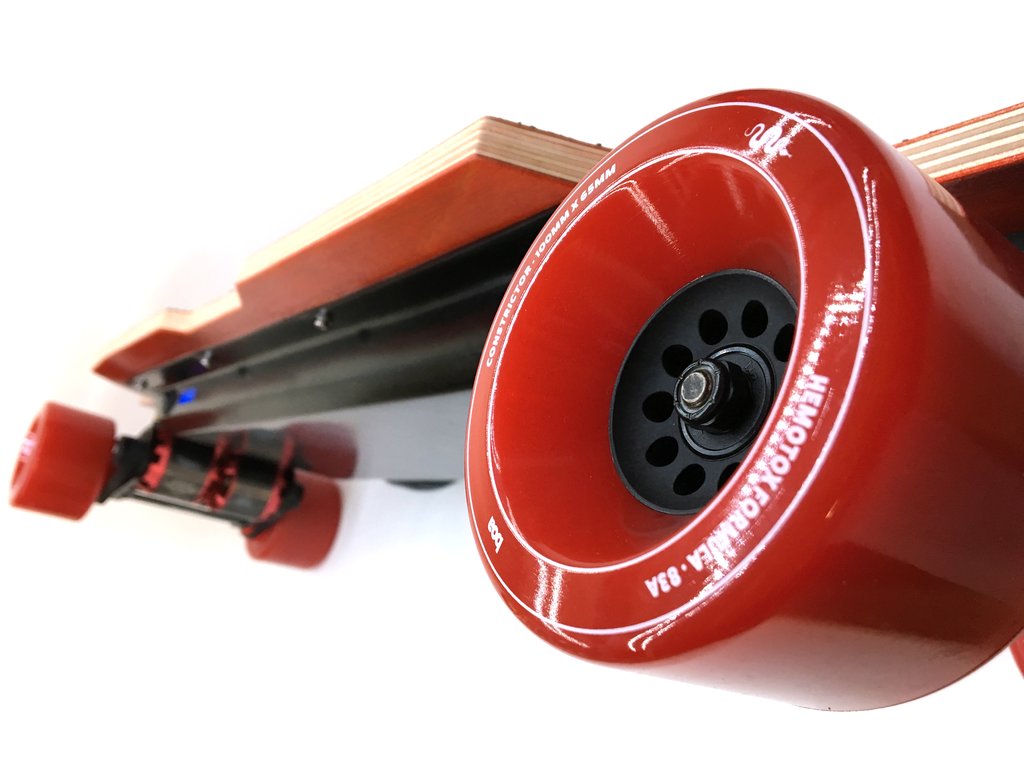
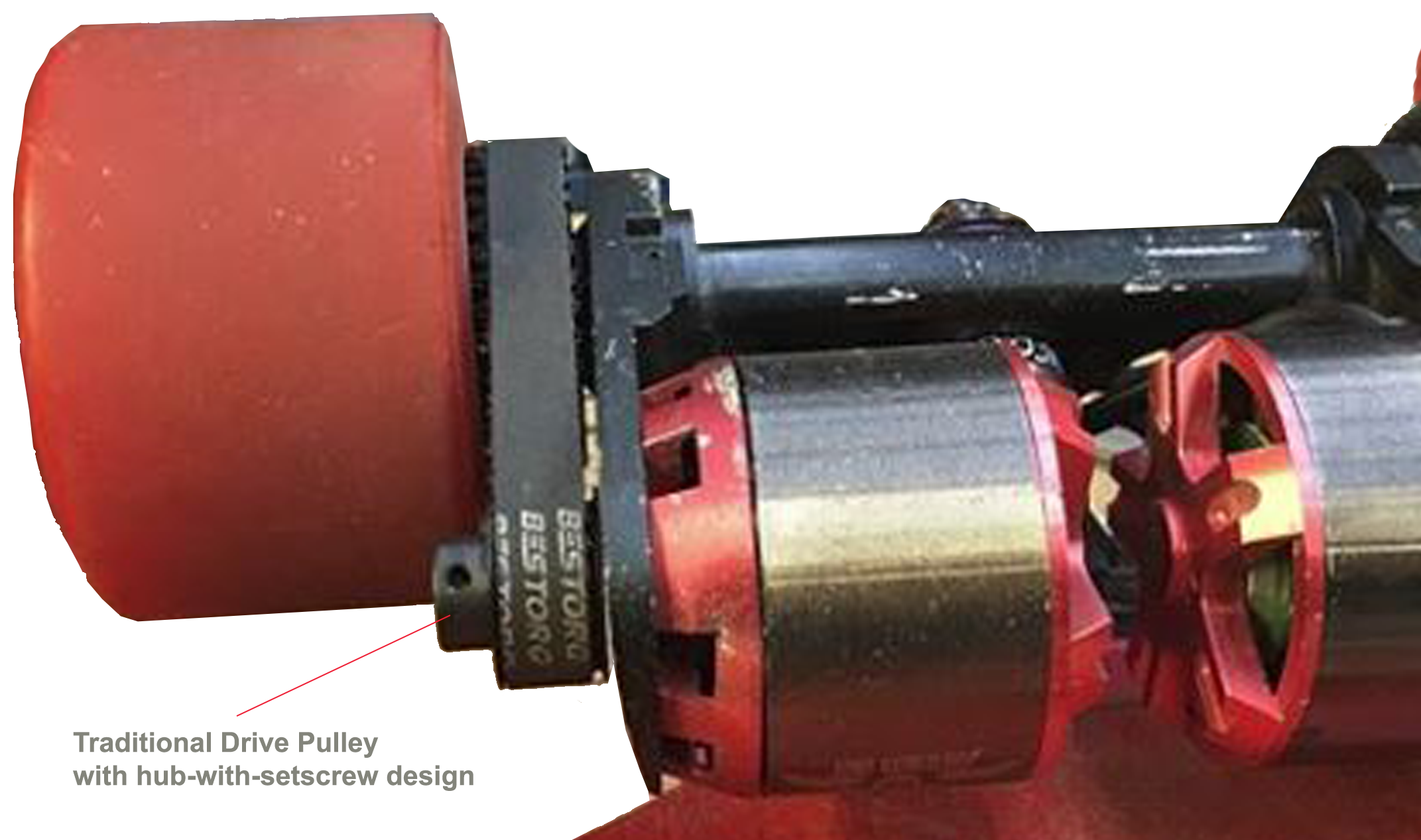
Damon's boards are painstakingly 100 percent custom-made. “I use my own branded 63mm sensored 190KV motors and the finest quality parts designed to carry a fully grown adult at ridiculous speeds on a skateboard. Aircraft grade machined aluminum motor mounts and pulleys, ceramic bearings, Calibre II trucks, my own hand-made high capacity battery packs using Samsung or Sony 18650 cells, Boa wheels, and hand crafted hard rock maple decks that I press myself, and high impact fiberglass electronics enclosures.”
One serious challenge faced by Mr. Wood was the size of a traditional drive pulley, which typically included a hub-with-setscrew design. This caused clearance issues with the drive wheels as the hub would stick out too close to the in-motion components.
CMT's Solution
Damon began to search the internet for a solution to this major flaw and found that Custom Machine and Tool Co., Inc. (CMT) in Hanover, Massachusetts had the ability to meet his specifications and go one step further.
Originally, Custom Machine and Tool Co., Inc. and Wood attempted to include the Concentric Maxi Torque bushing into the part design. However, there were irreconcilable compromises based on the space restriction and necessary torque requirements; this concluded that the part would not be an applicable candidate for the keyless hub-to-shaft bushing. Alternatively, a traditional approach was recommended by CMT to drill the setscrews through the pulley grooves in order to work within the space requirement and retain the torque needed for consistent operation. This compromise conquered the challenge faced by Mr. Wood to increase confidence in a final design.
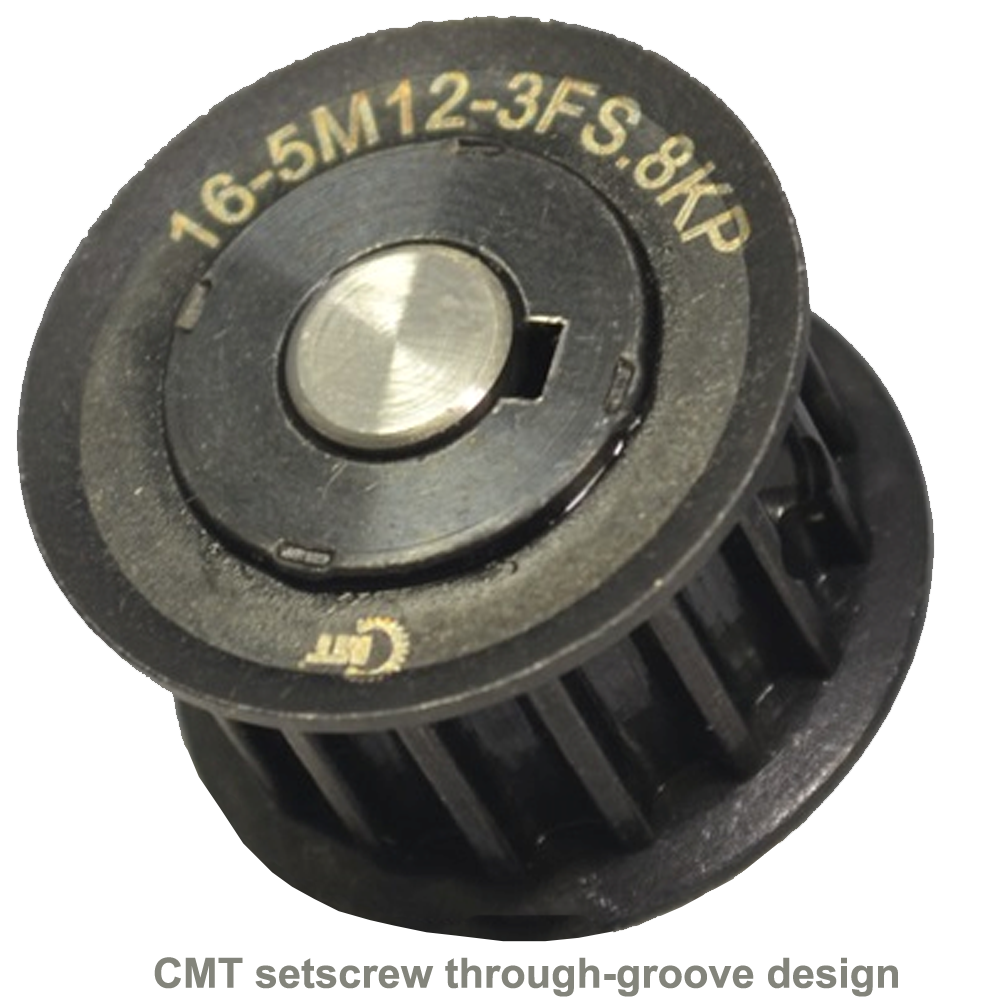
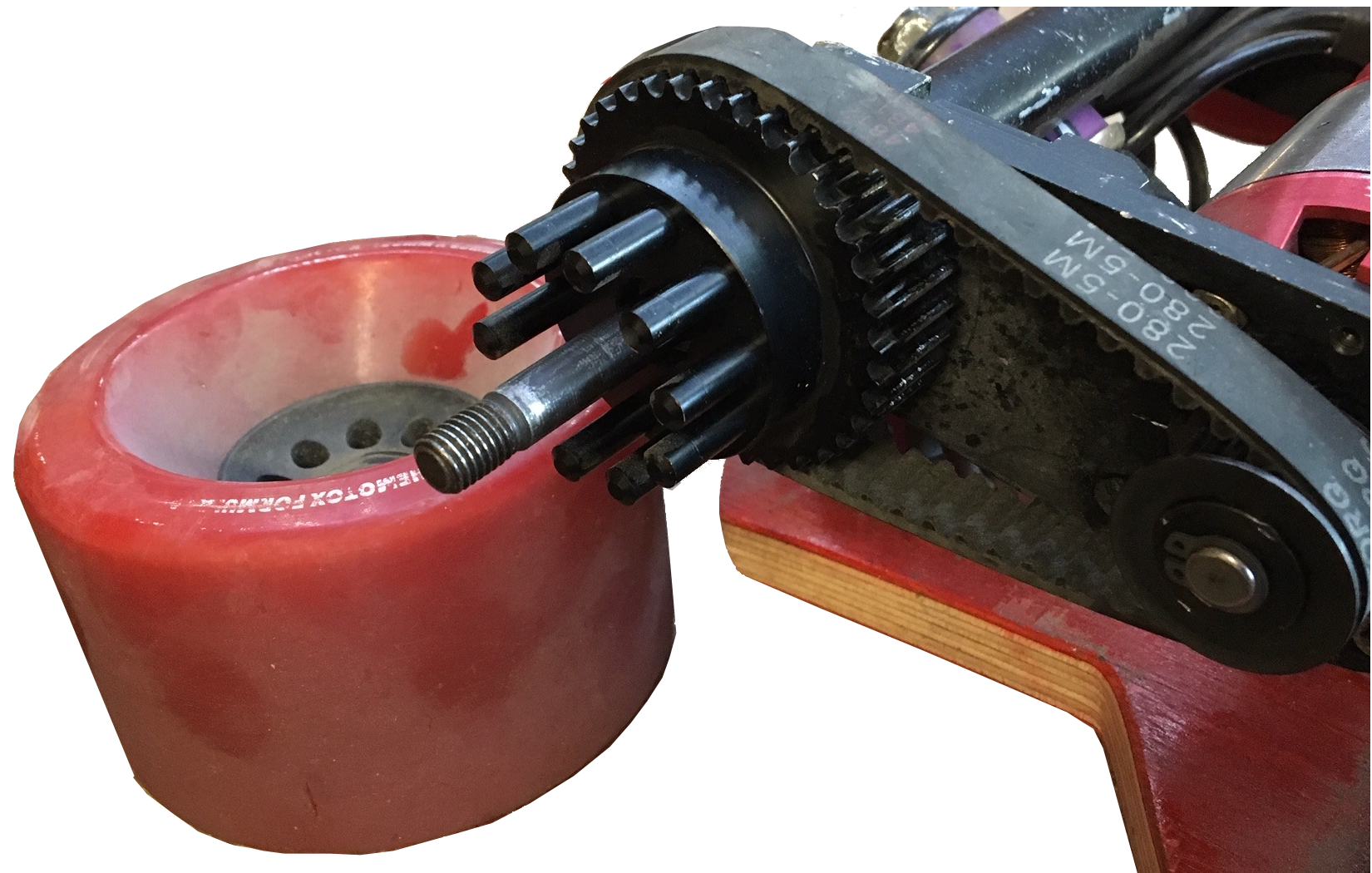
CMT was able to eliminate the current hub portion of the pulley and create a setscrew through-groove design, thus clearing up space around the drive system which brought added confidence and extraordinary efficiency.
Need a solution for your challenge? Contact us at: info@cmtco.com.